Для тех, кто следит за рынком коммерческих автомобилей, минувшие два года запомнились молниеносным обновлением модельной линейки Горьковского автозавода. В 2013 году появилась принципиально новая «полуторка» – «ГАЗель NEXT», затем – две модификации на ее базе, грузопассажирская и автобус. В 2014 году был представлен новый универсальный среднетоннажник «ГАЗон NEXT», а уже в марте – его семиместный вариант с двойной кабиной и городская модификация. Такой скорости обновления моделей не было и в советские времена, чего уж говорить про постсоветские годы. Появлению новых машин предшествовали масштабные изменения на производстве. Они особенно заметны в цехах штамповки, сварки и окраски автомобилей.
– С одной стороны, мы должны были установить современное оборудование и обеспечить высокий уровень автоматизации, чтобы гарантировать качество новых автомобилей, – вводит вашего корреспондента в курс дела Президент «Группы ГАЗ» Вадим Сорокин. – С другой, затраты должны были быть не слишком большие, чтобы сохранить цену автомобилей на возможно более низком уровне. Ведь для покупателей коммерческой техники по-прежнему главное – окупаемость. Еще больше усложняла задачу необходимость одновременно производить машины и нового, и предыдущего поколения: на них тоже сохраняется значительный спрос...
Чтобы пройти по этой тонкой грани, компании пришлось внедрить систему гибкого производства, которая позволяет делать в одном потоке сразу несколько разных моделей, быстро меняя номенклатуру в зависимости от спроса.
В ОЖИДАНИИ «УРАЛА NEXT»
Свою экскурсию по заводу я начал с цеха сборки и сварки кабин. Моим экскурсоводом стал директор по производству завода Андрей Софонов. Здесь изготовляют кабины для 9 различных модификаций грузовиков, из них 8 свариваются в одном потоке. Отдельно идет лишь кабина для старого среднетонажного ГАЗ-3309, которая серьезно отличается конструктивно. А скоро здесь появятся еще и кабины для «Урала NEXT».
Из 85 000 автомобилей ГАЗ, проданных в 2014 году, здесь начали свой путь около 60 000 (остальные – это фургоны и микороавтобусы – сваривают в отдельном цехе). Все это делают 203 человека в две смены.
На стенде у входа наглядная схема старых и новых линий. Цех был запушен еще в 1987 году и с тех пор там многое поменялось. Чтобы не создавать на рынке перебои с продукцией, модернизация проводится без длительных остановок производства. Используются новогодние каникулы, длинные майские праздники и так называемые корпоративные отпуска – когда весь завод уходит в двухнедельный отпуск. За это время устанавливается новое оборудование, перестраиваются линии конвейера, проводятся ремонтные и пуско-наладочные работы.
СТРАСТИ ПО КАБИНАМ
С запуском автомобилей семейства «NEXT» появилось более 250 наименований новых элементов кабины. Да, можно было построить новый цех, подвести к нему всю инфраструктуру и потратить на это огромные деньги, но это неизбежно привело бы к удорожанию автомобиля. Поэтому на ГАЗе пошли принципиально иным путем.
Сжимая участки по выпуску действующих продуктов, высвободили место для установки нового оборудования. Участки сварки и подсбора новых деталей нужно было разместить в непосредственной близости от основной линии конвейера, чтобы убрать затраты на транспортировку, снизить объем товарных запасов, увеличить скорость операций.
В ходе модернизации производства, в сварочном цехе было установлено новое оборудование южнокорейского производителя LG и немецкого Siemens, сварочные клещи американской Milko.
Особое внимание уделялось возможности быстрого перехода от одной модели к другой. Например, на одном участке происходит зафланцовка передних дверей «ГАЗелей «Бизнес» и «NEXT», которая идет при помощи двух прессов. Двери совсем разной конфигурации, однако использование новых механизмов смены штампов позволяет перейти на другую модель в течение 20 минут. И это не предел: технологи предприятия работают над тем, чтобы снизить время перехода до 5 минут.
– Весь процесс сварки максимально автоматизирован. При установке основания электроника сама определяет, какая модель стоит на линии и переходит на соответствующую программу. Это позволяет полностью исключить ошибки, связанные с человеческим фактором, – поясняет Андрей Софонов.
ПОВЕЛИТЕЛИ РОБОТОВ
Из-за многочисленных роботов-манипуляторов цех напоминает картинку из фантастических фильмов. Со стороны их движение – полный хаос. И не дай бог оказаться в зоне их работы. «Щупальца» роботов ходят по сложной траектории, места вокруг не очень много, поэтому приходилось рассчитывать траекторию фактически до миллиметра, что бы «руки» не столкнулись. Сами роботы немецкие – KUKA. С этим брендом ГАЗ работает давно, и нижегородские специалисты с этой техникой на «ты». Многие иностранные предприятия нанимают сервисные компании для программирования роботов. На ГАЗе это делают собственные специалисты, что обходится в несколько раз дешевле.
В цехе можно своими глазами наблюдать, как закладывается качество будущей продукции. Если посмотреть на кабины «Некстов», то они почти на 85% из оцинкованной стали, обладающей высокой степенью антикоррозионной стойкости. Это видно по блестящему оттенку металла. А на «Бизнесе» оцинкованы только детали основания – подножка, арки колес, кожухи фар, поскольку они наиболее подвержены воздействию агрессивной среды.
Кстати, кабинные модули у нового «ГАЗона»и «ГАЗели NEXT» одинаковые. Единственная разница – выпирающий моторный отсек у первого. Такая унификация позволила значительно сократить время на запуск производства, снизить объем инвестиций и, в конечном счете, сделать автомобили дешевле.
Вообще, гибкостью сварочного производства ГАЗ по праву гордится. В одном потоке идут кабины для «ГАЗели NEXT» и «ГАЗели Бизнес», среднетоннажных грузовиков «ГАЗон NEXT» и «Валдай». Все они могут быть как однорядными, так и двухрядными.
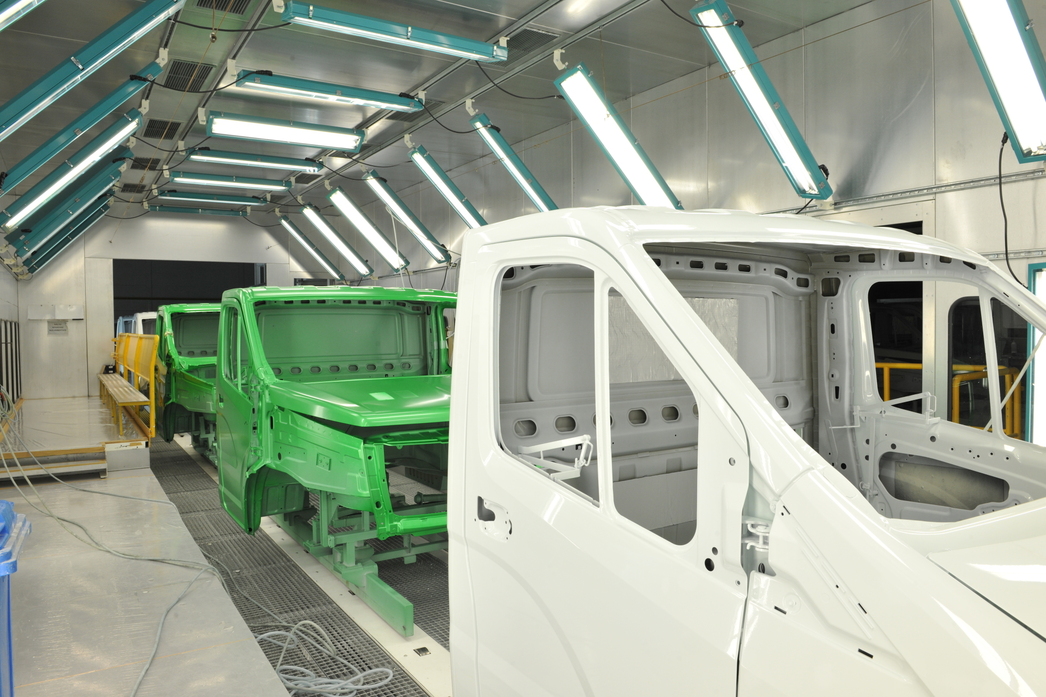
БЕЗ ЗАПАСОВ
Сваренная кабина нового автомобиля попадает в окрасочный комплекс. Автомобили семейства NEXT окрашивают в цехе Eisenmann, названном так по немецкому поставщику оборудования. Новенький цех – гордость завода. Введенный в эксплуатацию в 2013 году, он обеспечивает очень высокое качество лакокрасочного покрытия. Сфотографировать сам окрасочный процесс, к сожалению, нельзя: очень жесткие требования по чистоте воздуха не позволяют пускать в окрасочную камеру посетителей.
А мы тем временем попадаем в сборочный цех. Вход украшают огромные фотографии продукции: от ГАЗ-АА до нового «ГАЗона NEXT». Так же как и в сварочном цехе, за 2 недели до начала очередного месяца сюда приходит жесткая «закладка», определяющая, какие модели и в какой последовательности будут собираться на конвейере. Такую же «закладку» получают и поставщики, причем как внутризаводские (ГАЗ имеет собственное мощное автокомпонентное производство), так и внешние. Это позволяет определить, сколько деталей и в какое время нужно поставить на каждый участок конвейера.
ПРИНЦИП ХЕЙДЖУНКА
Для определения очередности установки машин на сборочную линию действует принцип «Хейджунка». Это почти искусство. Специалисты определяют порядок чередования более трудоемких и менее трудоемких в производстве моделей так, чтобы обеспечить максимально сбалансированную и гармоничную работу конвейера на весь месяц.
Сам необычно звучащий термин – из лексикона производственной системы ГАЗ. Внедрять ее на предприятии начали в начале «нулевых», когда завод вместе с еще несколькими предприятиями вошел в состав промышленной группы «Базовый элемент». В основу газовской системы легла используемая почти во всем мире производственная система компании Toyota. Отсюда и японские названия.
ТАКОЙ ВОТ «КАНБАН»
Другой интересный принцип называется «тянущая система» (по-японски – «канбан»). ГАЗ не работает на склад – каждая машина, сходящая с конвейера, уже имеет своего конкретного заказчика. Под этот заказ рассчитывается абсолютно все – и скорость работы конвейера, и поставки запасных частей. То есть уже 20 апреля, например, становится понятно, сколько рулевых колонок и какого типа будут подвезены к конвейеру 20 мая, на какие автомобили они будут установлены и какому заказчику поступят.
Мы идем вдоль четвертой линии главного конвейера, где собираются среднетонажные «ГАЗоны» и «Валдаи». Начинается конвейер с аккуратно сложенных рам грузовиков, на которые впоследствии устанавливаются мосты и рессоры. Потом рама переворачивается в рабочее положение для установки двигателя, кабины и всех остальных узлов и систем.
Рядом с основной веткой – дополнительные «ячейки». Например, сборки сидений, оперения, подсборки двигателей. Деталей собирается ровно столько, сколько необходимо на данный момент. Больших запасов здесь не держат. То же самое – на участке установки колес. Их чуть более двух десятков: огромные для внедорожников «Садко», поменьше – для универсальных машин и еще меньше для новой модели для городских перевозок «ГАЗон Сити». По мере использования запаса новые колеса подвозятся к участку.
ПОСМОТРИ В ЗЕРКАЛО!
По цеху непрерывно курсируют малютки-погрузчики, которые и подвозят необходимые детали. Здесь целая дорожная сеть, с выделенными полосами, пешеходными дорожками и переходами. Правила движения – не менее строгие, чем на улицах. Для безопасности на колоннах установлены огромные сферические зеркала, позволяющие видеть, что происходит за твоей спиной.
– До внедрения новой системы запасы деталей у конвейера достигали двух недель. А это – высокие издержки и плохая организация рабочего пространства. Сейчас запас по большинству деталей – 2 часа. По крупногабаритным – таким, как колеса, обшивка кабин и панели приборов – на 30 минут, – поясняет Андрей Софонов.
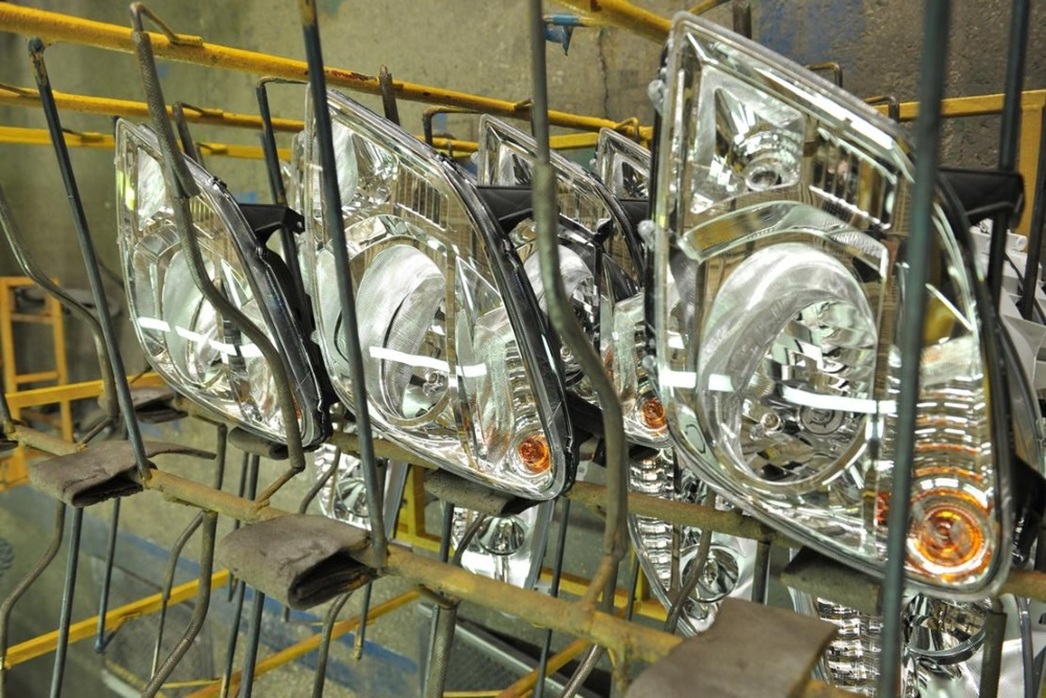
КАК ИГРАЮТ «СВАДЬБЫ»
Отдельная ячейка посвящена двигателям «ГАЗонов» (черный минский – для ГАЗ-3309 и синий ЯМЗ – для NEXT. Двигатели приходят уже собранными, но рядом с конвейером на них устанавливается навесное оборудование, ремни, жгуты, коробки передач, заливается масла.
Дальше – участок, где собираются кабины. Устанавливаются стекла (либо вклейка на герметик, как на «ГаАЗоне NEXT», либо, как на старой модификации, – на резиновый уплотнитель). Затем – панели приборов и обивка. Здесь разница между двумя модификациями среднетонажника еще ярче: спартанская отделка старой версии и вполне современная и комфортная – новой. А вот с «ГАЗелью NEXT» у нового «ГАЗона» интерьер почти идентичен. Отличаются лишь сиденье водителя, кнопки на панели приборов, да рычаг КП.
Собранные кабины захватываются специальным подъемным устройством и ставятся на раму. Эта почти ювелирная операция на конвейере называется «свадьба». Требуется немалый опыт, чтобы одним движением поставить тяжелую кабину точно на место.
«ЦЕПОЧКА ПОМОЩИ»
Скорость движения конвейера и, соответственно, суточный темп производства становятся известны уже при определении месячного объема заказов. Высококвалифицированные бригадиры, кнаизусть знающие все малейшие нюансы операций в своем производственном вене (официально их называют «лидеры»), заранее подготавливают рабочие места под темп сборки и прикидывают алгоритм действий так, чтобы рабочие успевали произвести все необходимые манипуляции и не бегать за конвейером. На одного «лидера» приходится 6-10 человек, которых он в любой момент может подменить.
– На случай возникновения проблемы, есть четкао прописанная «цепочка помощи», в которой определены все уровни ответственности и схемы взаимодействия разных подразделений. Заметив неисправность, рабочий включает сигнальную лампочку и останавливает конвейер. Бригадир видит это и подходит разбираться. Если проблема в течение 10 минут не решилась, то подключается начальник цеха. Если и он в течение 20 минут ничего не может сделать, подключается директор по производству и на своем уровне решает проблему, подключая ответственных из всех необходимых служб, комментирует Андрей Софонов алгоритм действий в нештатных ситуациях.
На многих рабочих местах висит изображение перевернутого треугольника на красном фоне. Значит, здесь выполняется важная операция, которая в будущем влияет на безопасность водителя и пассажира. Как правило, это крепления с требуемым моментом затяжки или, например, установка моста и рессоры, ремней безопасности.
ПЛЮС «ВОДЯНОЙ ТЕСТ»
Весь сборочный цикл занимает до 3 часов. Длина конвейера – 360 метров, на них расположено 26 станций, по которым проходит автомобиль. В сборочный процесс встроены 7 контрольных точек. Здесь специалисты дирекции по качеству проверяют соответствие всех работ конструкторской документации. Например, перед «посадкой» кабины контролируются все соединения, доступ к которым будет впоследствии затруднен. После схода с конвейера машина проходит обкатку на специализированных стендах. Проверяются работа двигателя и электрооборудования, рулевой системы, тормозное усилие, СО и СН, величина зазоров и качество лакокрасочного покрытия, регулируется свет фар. В финале: тест на герметичность в специальной водяной камере.
Рядом с ней уже стоят новые «ГАЗоны». Угол подачи воды из форсунок и ее давление строго просчитаны под все возможные погодные аномалии. Сам по себе «водяной тест» – яркое и эффектное зрелище. Особенно для фотографов.
После прохождения всех тестов машина готова – отправляется на склад перевозчика, а затем – в дилерские центры по всей России и за рубежом.